Green plastics: the solutions are here
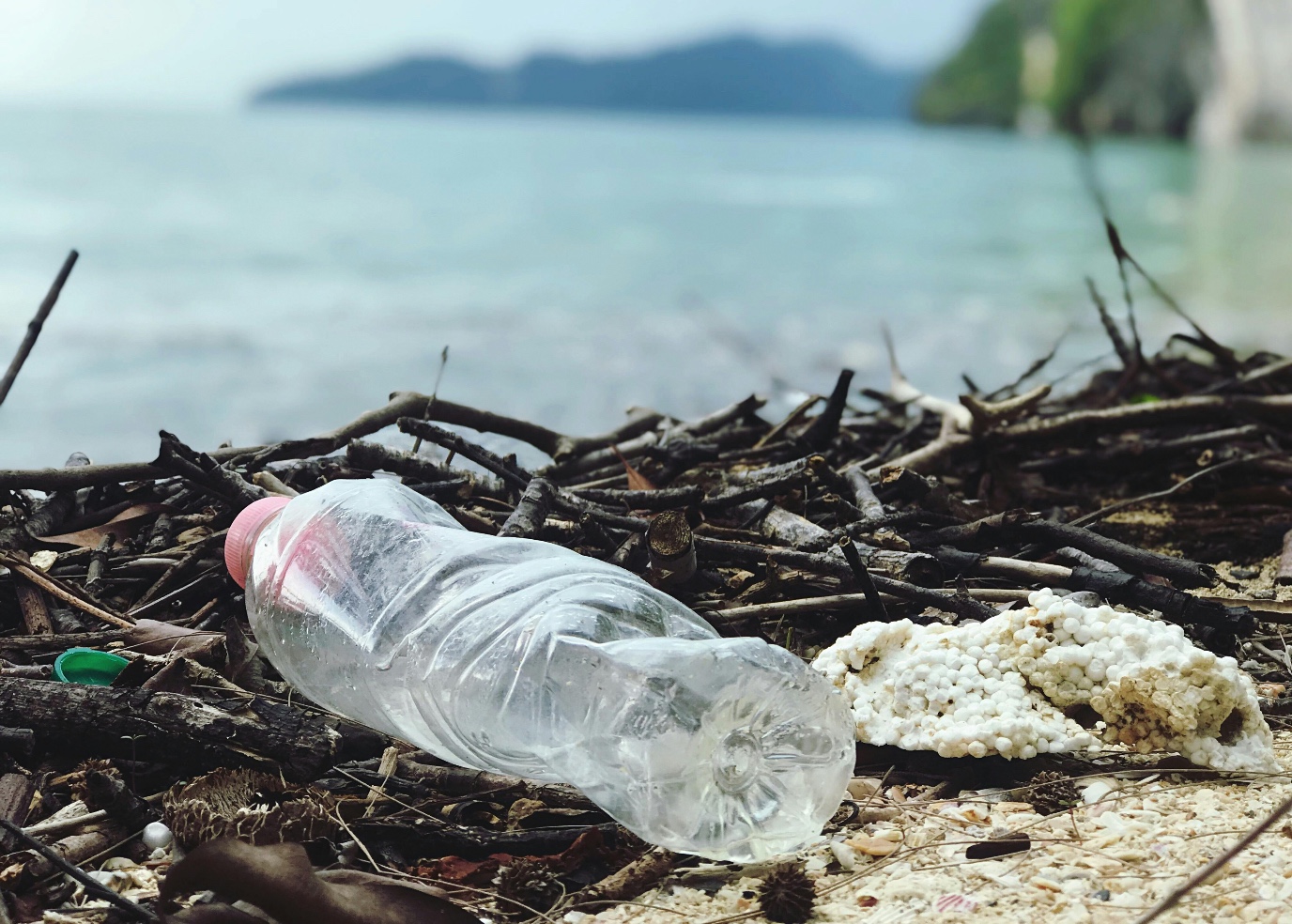
Plastics are incredibly convenient, but also generate a lot of waste. And they are usually made from fossil raw materials, which is bad for the climate. Bio-plastics from vegetable raw materials are an alternative, but how do you make truly green plastics? Scientists at the Faculty of Science & Engineering are working hard on that. This is the first in a series of four articles on plastics research within this faculty.
FSE Science Newsroom | Text René Fransen
‘If you want green plastics, you have to take their entire life cycle into account,’ says Katja Loos, Professor of Macromolecular Chemistry at the University of Groningen. ‘From the source of the raw materials, via the synthesis of plastics, to the production of plastic products and their end-of-life.’
Plastic bottles made from biomass
Plastics are polymers, long chains of one or more types of building blocks: monomers. These monomers can be made from fossil feedstock, but it is also possible to use renewable carbon sources, explains Vincent Voet. He is a scientist in the Circular Plastics research group at NHL Stenden University of Applied Sciences, which has formed a joint research group called HyBRit with Loos’s team. ‘Plastics can be made from biomass, carbon dioxide, recycled materials.’
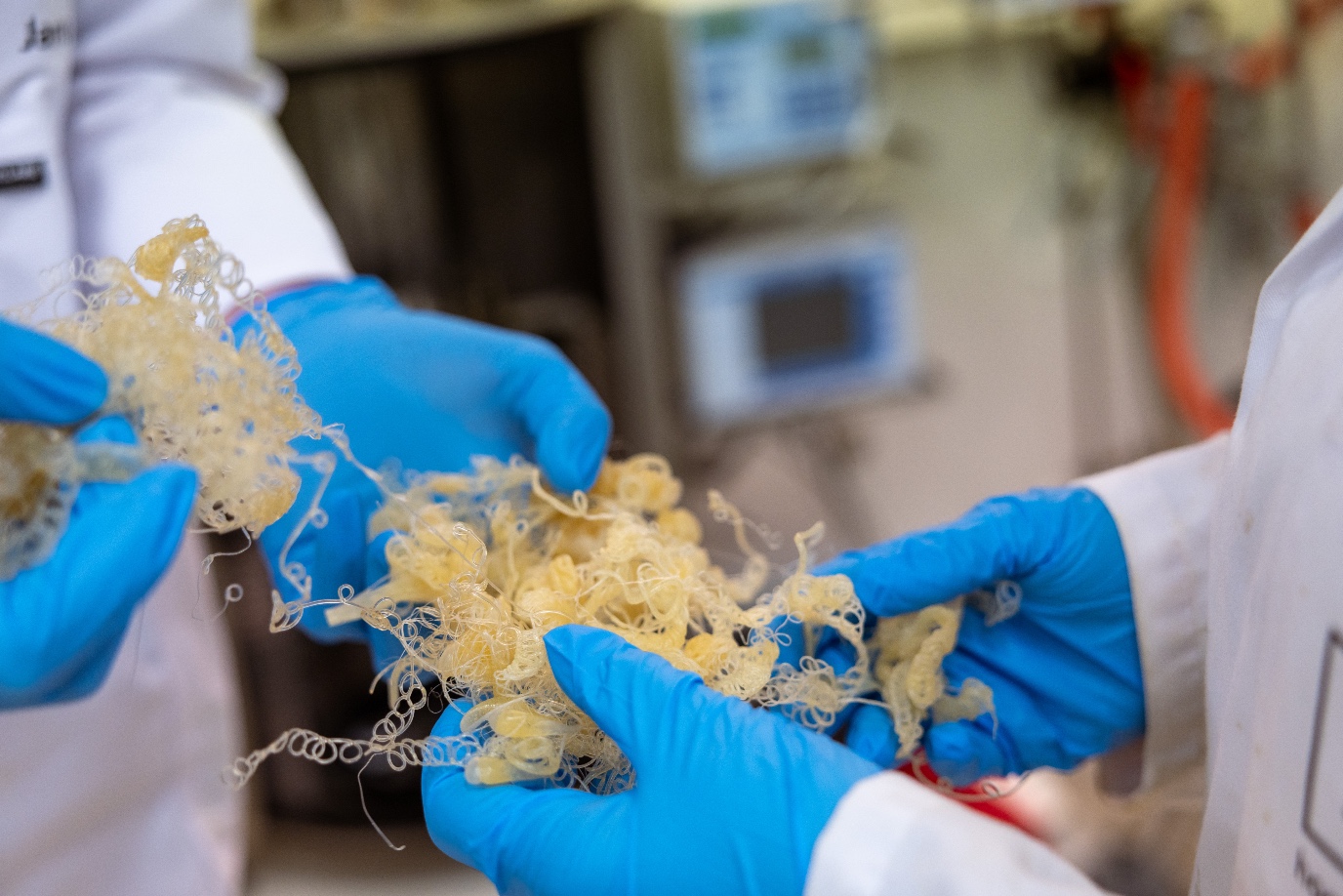
One of the main focus areas of the group is the production of polymers from bio-based building blocks. Voet: ‘Our two universities are located in the Northern Netherlands, an area with a lot of agriculture but also academic expertise and a well-established chemical industry. When you’re making plastics, it is an advantage if you can source your raw materials locally.’
Sugars are one interesting source for polymer production. Voet: ‘There are many waste streams from agriculture that provide starches, cellulose, or other polysaccharides.’ These can be turned into furanics, for example, which yields biopolymers like polyethylene furanoate (PEF), an alternative for PET (polyethylene terephthalate). PET is the polymer most commonly used for plastic packaging.
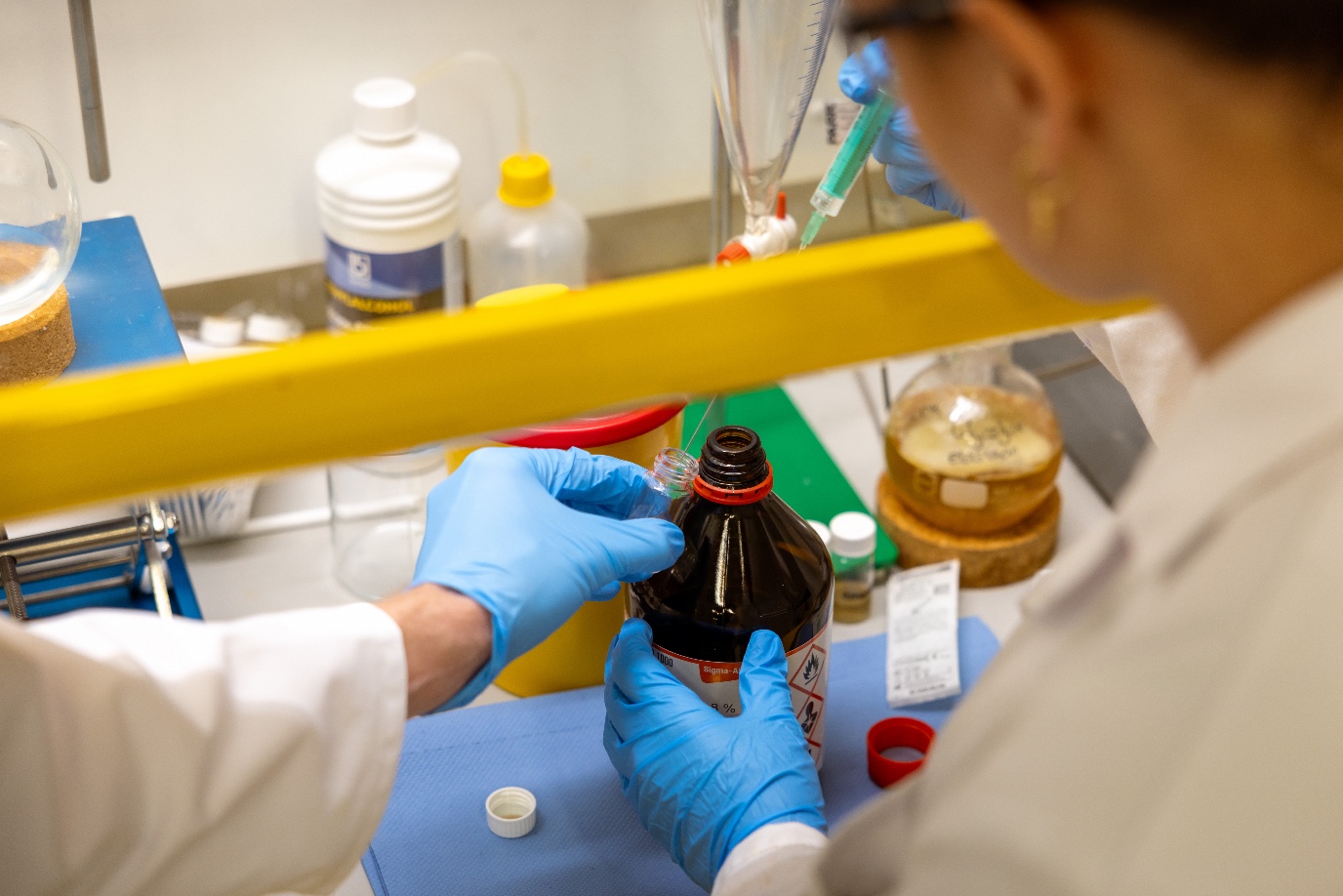
Hybride onderzoeksgroep voor polymeerwetenschap
HyBRit is a collaboration between the University of Groningen and NHL Stenden University of Applied Sciences, supported by the University of the North.
The team combines fundamental and applied research, and shares staff, students, and facilities. This combination makes it easier to, for example, scale up a process from a basic science lab producing perhaps a few grams of green plastics to an industrial process producing tens of kilograms. Thanks to the collaboration, the required knowledge and equipment for this upscaling is already present at the start of each project.
The group was established in 2020 and has published a range of joint scientific papers. The latest one describes the process of recycling super strong aramid polymers known under the brand names Twaron or Kevlar.

Plastic from paper waste
Other renewable sources that are being researched at the University of Groningen are recycled polymers. Dina Maniar, assistant professor of Polymer Chemistry, works together with the paper industry, which produces a lot of lignin and cellulose waste. ‘They would like to make something useful from these waste streams. We are looking into ways to turn this into a bio-based composite.’
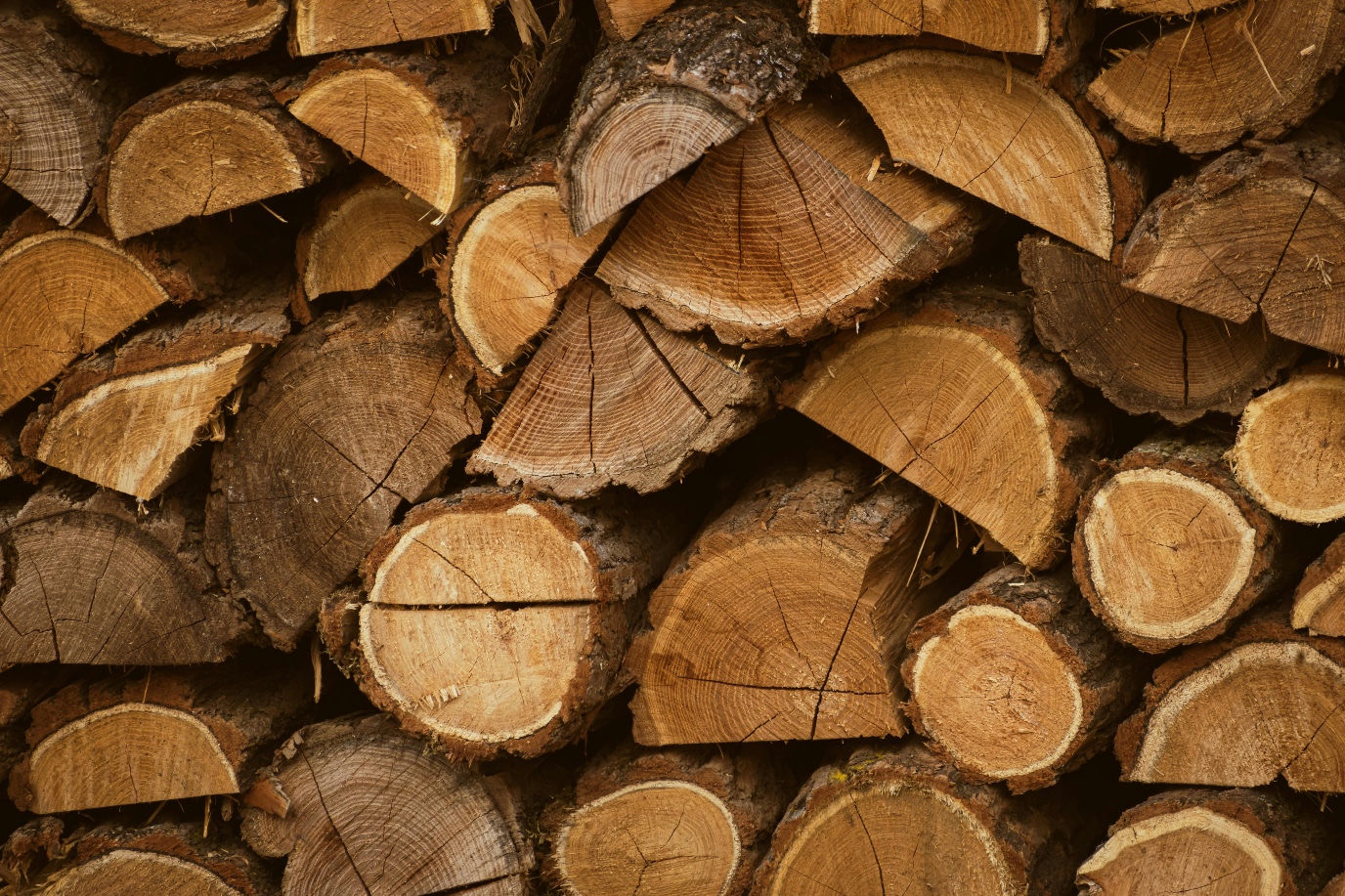
Maniar is also looking for greener chemical processes. The traditional way to polymerize—i.e. to get from separate monomers to a long polymer string—is through a chemical process that requires toxic solvents and high temperatures. Maniar: ‘We use enzymes for the polymerization as these work in water at much lower temperatures.’ An added advantage of enzymes is that they offer greater control over the polymerization process. This helps her to make polymers with specific properties, e.g. to be used for solar panels in the national consortium SolarLab.
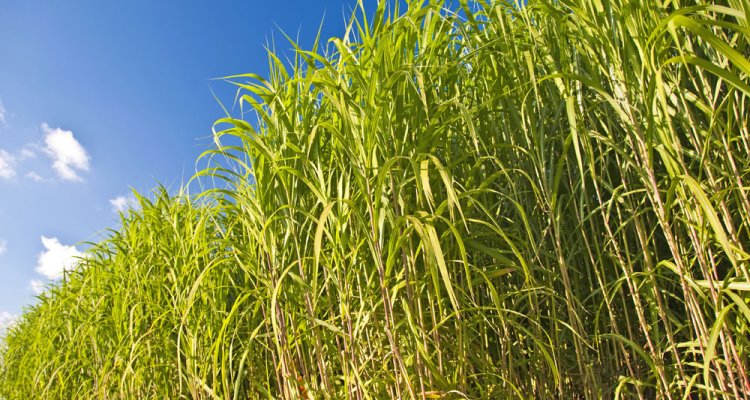
One example is a sugar-based polymer that is used for support in solar panels. ‘This polymer must be able to resist exposure to all kinds of weather, and it has to be durable.’ In a similar project, Maniar is working on polymers from elephant grass which might be used in very light-weight solar panels intended for roofs that are not strong enough for conventional panels.
She also thinks ahead, about what to do when the plastics have served their purpose. In the case of the composite, this is complicated: ‘In these materials, the polymers are crosslinked. This makes them strong, but these crosslinks are very hard to break. It takes quite a bit of fundamental research to find ways to de-crosslink the polymers so they can be reused.’ Maniar has succeeded in recycling crosslinked lignin, but it is hard to remove the crosslinks in lignin-cellulose composites. ‘We are not yet sure what is going on there.’
Biodegradable plastics
One way to eliminate plastic waste is to make biodegradable plastics that will decompose into carbon dioxide and water. However, this is not as straightforward as it may seem. There are many types of biodegradation: rapidly degradable in soil, degradable in salt or fresh water, degradable on your own compost heap, or in an industrial composting facility (at 60˚C). These different types of plastics need different processing, so they must be separated in waste streams.
Something to remember: bioplastics—made from natural sources such as sugars—are not necessarily biodegradable! For example, polylactic acid-based plastics will not fully decompose in the soil.
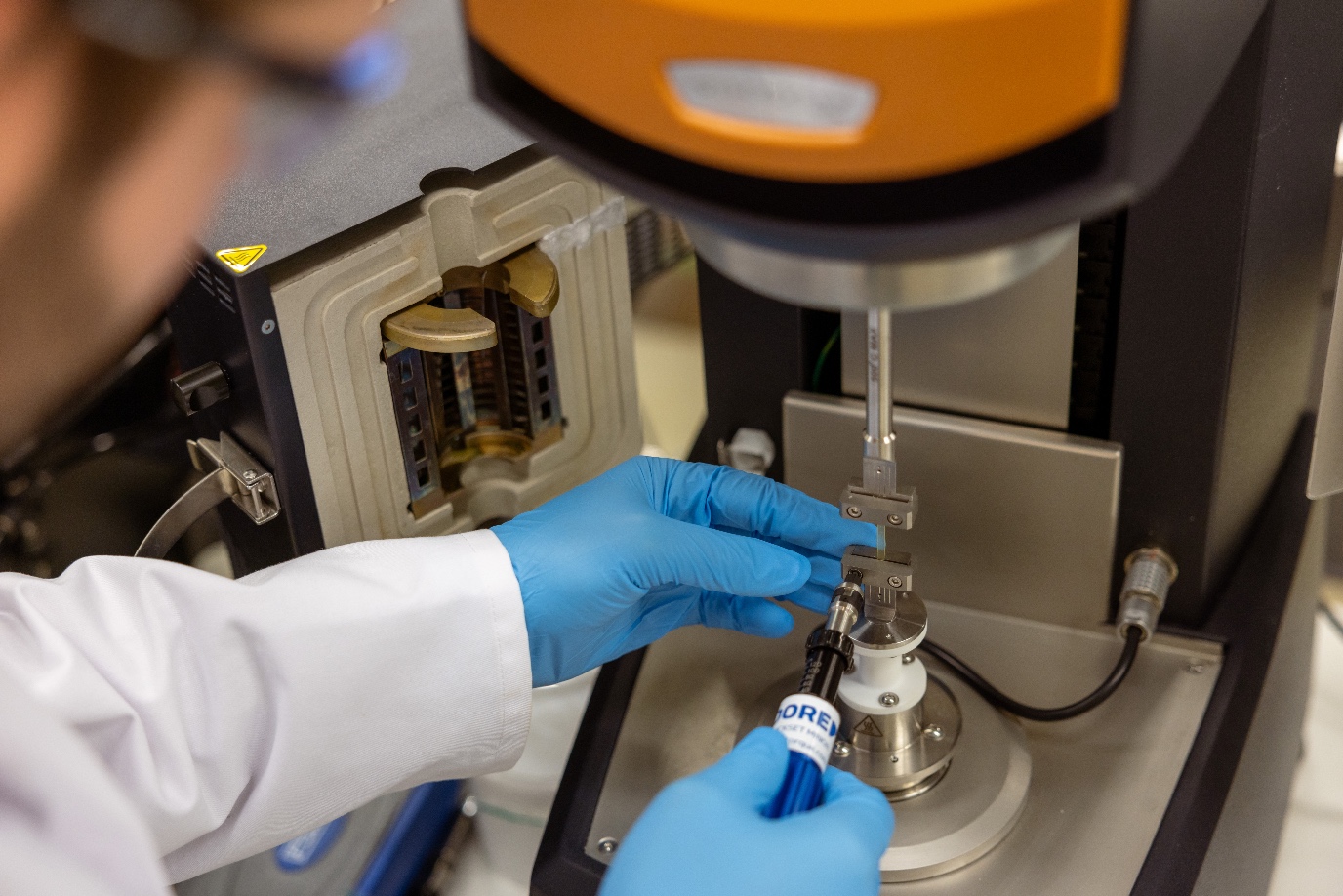
From plastic to product
There are green alternatives for the entire production process of plastics. However, translating these scientific discoveries into a commercial product proves difficult. Voet: ‘One major challenge is that the traditional processes for plastic production have been around for about a century. These processes have been fine-tuned all that time.’ The new green alternatives often require a different, and less well-developed, infrastructure, which means that green plastics are usually a bit more expensive.
Loos adds: ‘Building a factory for green, enzymatic production requires major investments. The technical solutions are there, but adoption requires regulations set by the government, or even better, by the European Parliament.’ She points out that this has been done before: ‘Seatbelts have been made compulsive in cars. And when it was discovered that chlorofluorocarbons—the propellants in spray cans—are responsible for the hole in the ozone layer, they were banned.’ Green plastics deserve this support as well. And it would not be bad for industry, Loos thinks: ‘A company that starts making the switch towards green plastics now will be in the lead in ten years’ time.’
This is the first in a series of four articles on plastics. Next week and the week after, you can read about research on plastic recycling. And in three weeks, we will discuss how dangerous microplastics are, and how we can prevent their creation.
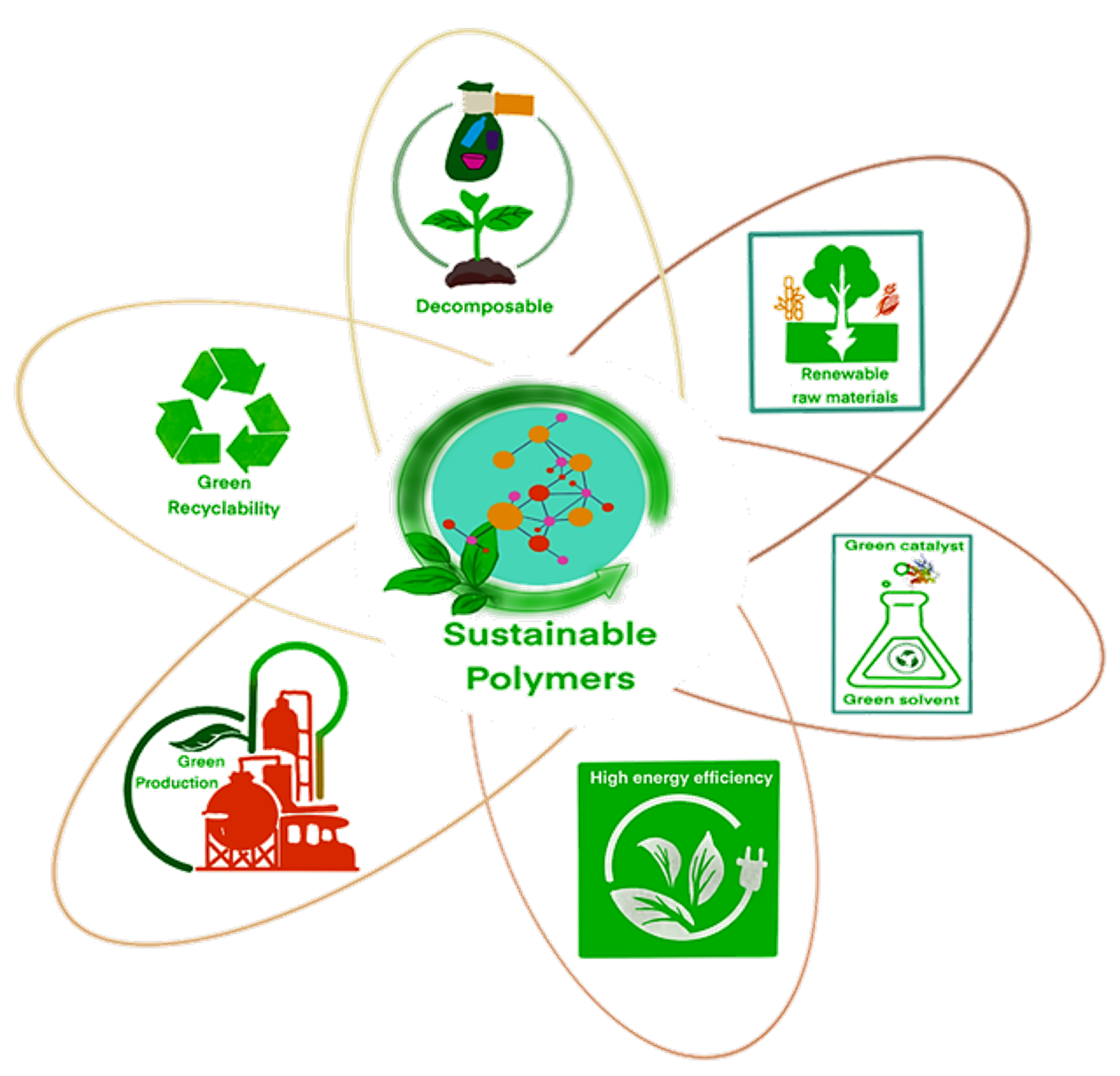
Last modified: | 03 April 2025 10.51 a.m. |
More news
-
03 April 2025
IMChip and MimeCure in top 10 of the national Academic Startup Competition
Prof. Tamalika Banerjee’s startup IMChip and Prof. Erik Frijlink and Dr. Luke van der Koog’s startup MimeCure have made it into the top 10 of the national Academic Startup Competition.
-
01 April 2025
NSC’s electoral reform plan may have unwanted consequences
The new voting system, proposed by minister Uitermark, could jeopardize the fundamental principle of proportional representation, says Davide Grossi, Professor of Collective Decision Making and Computation at the University of Groningen
-
01 April 2025
'Diversity leads to better science'
In addition to her biological research on ageing, Hannah Dugdale also studies disparities relating to diversity in science. Thanks to the latter, she is one of the two 2024 laureates of the Athena Award, an NWO prize for successful and inspiring...