Innovation leads to savings
The idea of producing more silt from waste water as a bio-commodity for generating sustainable energy may seem incredible, but Prof. Michel Boesten , professor of Chemical Engineering at the University of Groningen, thinks that this will soon be a cost-saving, environmentally friendly alternative when purifying waste water in sewage treatment plants.
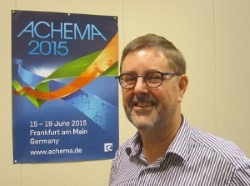
Sustainable energy from incinerating silt
Boesten: ‘Dutch water authorities spend more than € 200 million per year on the process of draining, discharging and incinerating silt, which is a high price tag for an activity that is not even among the water authorities’ primary tasks. In the past, silt was simply sprayed onto farm land and used as a fertilizer. The presence of heavy metals and pathogens in sewer silt means that this practice has now been banned. In the Nether-lands, silt is processed in incinerators or cement ovens. It is time for a sustainable alter-native for silt processing, one that will save money for the water authorities.’
Boestens’ solution
‘The solution is actually quite simple: produce more sewer silt, so that it can be used as biomass for raw materials and fuel. By making greater use of biomass as renewable energy, the average water treatment plant could save several million euros per year on its bills. Easy money.’
The silt problem
Boesten: ‘Silt has to be drained. Producing more silt would only be feasible if mechanical draining (the process whereby water is drained from the organic and inorganic dirt particles in the silt) were to be substantially improved. The silt must also be dried before a client is prepared to incinerate it. Drying silt from sewage treatment plants with 80% water is an expensive business, which not only requires a drying facility (investment), but also involves new safety risks (risk of fuel and gas explosions) and increased CO2 emissions. Producing more silt at a higher cost is a non-starter. Silt must be made to generate income.’
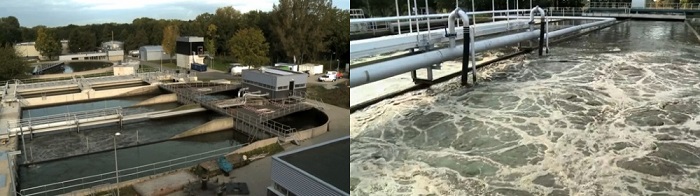
Boestens’ solution (2)
‘We studied and developed the idea of adding coal dust to the silt, which can signi-ficantly improve the mechanical draining process. This addition of inflammable solid matter not only increases the ratio of dry matter in the sewage silt, it also increases the calorific value of the drained silt. This shouldn’t pose a problem to incinerators as most incinerating plants burn inflammable substances these days, including coal.’
How did you end up in the water treatment world?
Boesten: ’For the last ten years, I´ve been working at DSM and the Department of Chemical Engineering in the University of Groningen, studying integrated water management as a means of sustainable energy-saving development. My work brings me into regular contact with companies and water authorities. Students of Chemical Engineering and Industrial Engineering & Management help to expand integrated knowledge of systems like this during their Bachelor’s and Master’s degree programmes, by conducting literature studies and tests in laboratories and companies.’
What is the next step?
Boesten: ‘We’re currently on the threshold of a very important development, of which I am incredibly proud. A major research programme, in which numerous interested parties (including the Foundation for Applied Water Research (STOWA) and the Noorderzijlvest water authority) took part, will be concluded in December. The research looks into methods for draining silt from sewer water treatment by adding incompressible particles, such as coal dust. The added particles probably strengthen the structure of the silt briquette so that it ‘clogs up’ less easily and allows the draining process to continue unimpeded.’
‘Furthermore, the Fryslân water authority is currently building a plant in Heerenveen, where coal dust will be added to silt for 50% of the capacity. The next step is to optimize the processes and expand our knowledge. All parties involved in the research (the water authority, coal suppliers and incinerator operators) are in agreement and believe in the project. Once the plant is operational, I’ll recruit students to carry out further research. Exciting.'
Cooperation
Prof. Michel Boesten cooperates with René Finkers from Research & Valorisation and Prof. Gert Jan Euverink, director BioBrug . The company Water & Energy Solutions , which is owned by Aaldrik Haijer, who studied Chemical Engineering at Groningen, helps Boesten with the process supervision aspect of research projects .
Last modified: | 15 October 2024 11.10 a.m. |
More news
-
04 July 2025
University of Groningen awards various prizes during Ceremony of Merits
The UG awarded different prizes to excellent researchers and students during the Ceremony of Merits on 4 July 2025.
-
02 July 2025
Relinde Weil reappointed as a member of the Supervisory Board UG
The Minister of Education has reappointed Relinde Weil for a second term as a member of the Supervisory Board of the University of Groningen.